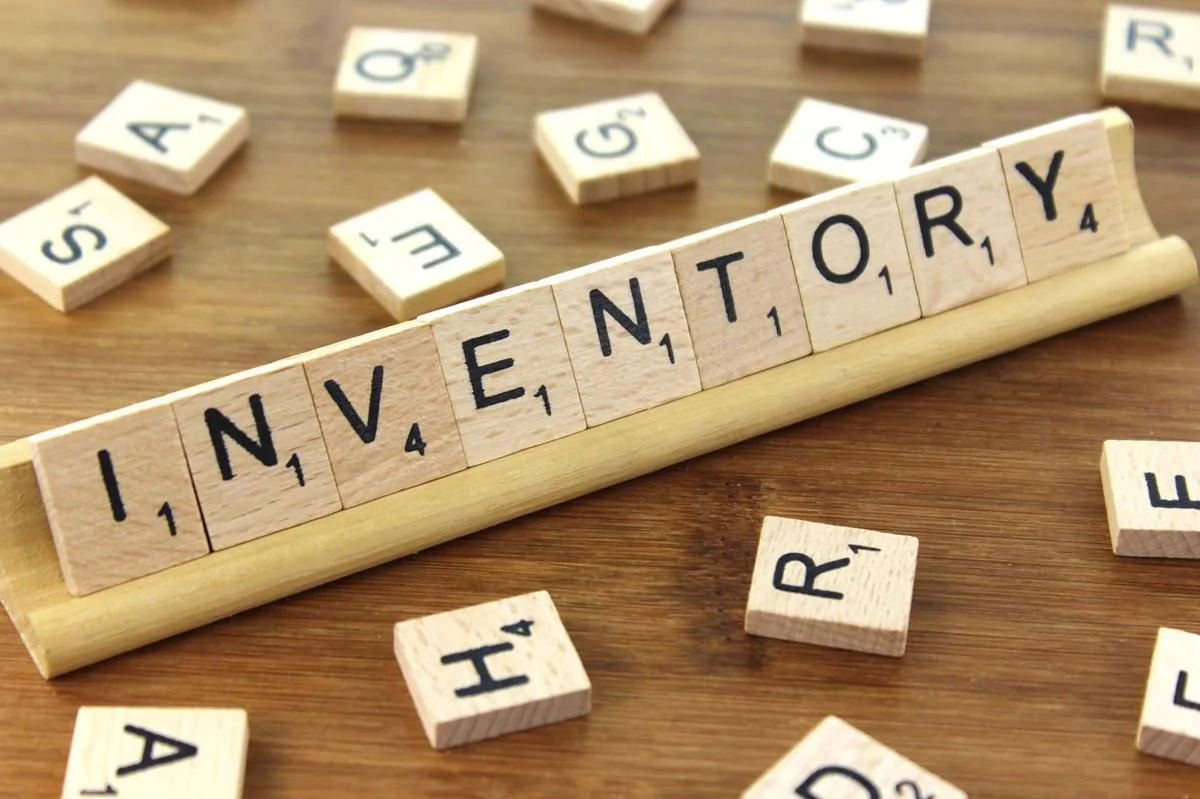
Different Inventory Types: From Raw Materials to Finished Goods
Different Inventory Types: From Raw Materials to Finished Goods
As products go down a manufacturing line, every added cost and inefficiency eats into the profit margin. It’s why lean manufacturing has become essential for all businesses to survive in an ultra-competitive global economy.
Fortunately, businesses can track each of these costs and inefficiencies through their accounting for manufacturing inventory processes by using inventory management software. Businesses can categorize materials as they move through the process, from being raw materials to works-in-progress, and finally a finished products.
Without such precise tracking, it’s likely that businesses will find their bottom line lacking at the end of the year.
1. Raw Materials Inventory
Raw materials inventory involve items used to make finished products. Raw materials can be commodities or components that businesses buy or extract themselves. In sum, they’re all the stock that hasn’t been used for manufacturing yet. For accounting solutions purposes, raw materials are considered an inventory asset, debited to raw materials and credited to accounts payable. There are two different categories of raw materials — direct and indirect.
The formula to calculate the total cost of your raw materials inventory is:
-
Total Raw Materials = Beginning inventory + Purchases added – Ending inventory
Let’s say you own a scooter manufacturing company. For this quarter, your starting inventory was worth $20,000. During this period you bought $34,000 worth of raw materials. At the end of this quarter, your raw materials on hand were $18,000.
-
Total = $20,000 + $34,000 – $18,000 = $36,000
As you’ll see, these inventory types follow the manufacturing process, from raw materials to works in progress to the finished products. Accounting for each stage of production helps portray an accurate picture of a manufacturer’s Cost of Goods Sold. For the raw materials stage, there are two categories of inventory, direct and indirect raw materials.
Direct Raw Materials
Direct raw materials are all the materials that make up the finished product. As an example, all the parts used to make a bed would be considered direct raw materials, from the wood to the metal frame and components like screws. Direct raw materials are considered a part of the cost of goods produced, which is then divided into the cost of goods sold and ending inventory.
Indirect Raw Materials
Indirect raw materials are materials that are consumed during the manufacturing process, but aren’t a part of the final product. Things like cleaning supplies, disposable tools, lubricants, and tape are examples of items that could be considered indirect raw materials.
Indirect raw materials typically fall under manufacturing overhead and are added to the cost of goods sold. If only a small amount of an indirect raw material is used, they are sometimes reported to an expense as incurred.
2. Work In Progress (WIP) Inventory
All inventory types used to create a finished product are considered WIP inventory. If you manufacture bicycles, all of the unfinished bikes in your shop could be considered WIP inventory.
You can also think of all the materials in use on a factory floor as WIP inventory. WIP inventory does not include raw materials sitting on the shelf or the finished goods that are ready for sale; they’re somewhere in between, and thus get the WIP designation.
When accounting for WIP inventory, it typically gets its own account entry on the general ledger and is an asset. Costs include the raw material costs, labour cost, and factory overhead.
Calculating the WIP inventory formula can be time-consuming and tricky, so most businesses try to minimize it before a specific reporting period. Businesses that follow a Just In Time (JIT) inventory philosophy typically have very little WIP inventory.
3. Finished Goods Inventory
As part of your inventory management solutions, finished goods are items that are ready for show time. They’ve been manufactured from raw materials or purchased from a supplier, and are ready to be sold to customers. Finished goods that are purchased as completed for sale are considered merchandise by retailers.
For accounting purposes, finished goods are short-term assets because of the expectation they will be sold as soon as possible. The finished goods inventory formula is a straightforward inventory ratio that can be used to calculate the value of your goods:
-
Finished Goods = (Cost of Goods Manufactured – Cost of Goods Sold) + Previous Finished Goods Inventory Value
For any one reporting period, finished goods are combined with raw materials and WIP inventory to make up the total inventory line item on a balance sheet.
4. Packing Materials Inventory
Packing materials inventory includes any items your business used to pack the products you sell. If you make toothpaste, the tube you put the toothpaste in could be classified as packing materials. Any boxes or packaging you use to ship or store your products are packing materials as well.
Final Thoughts
Properly accounting for manufacturing inventory through every step of the process is essential to running a profitable business. In a business environment increasing in complexity and with little margin for error, using an inventory management solution that brings order to chaos can mean the difference between ending the year in the red or black.